Et BILA forprojekt er en god investering når løsningen er kompleks
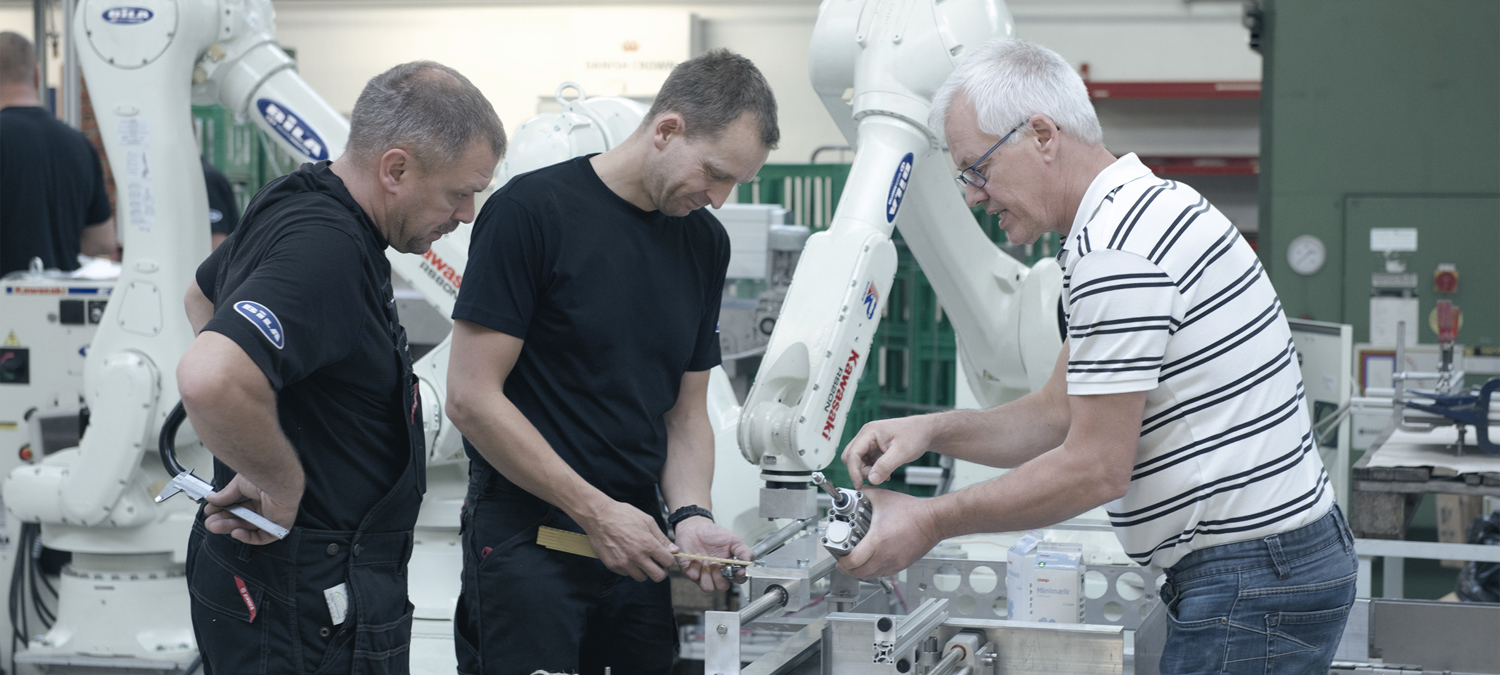
Forprojekt åbner op for godt partnerskab
Når man som kunde hos BILA ønsker en kompleks løsning, er der hurtigt mange spørgsmål, der melder sig. Derfor tilbyder BILA at lave et forprojekt i samarbejde med kunden. Ved et forprojekt afgrænser man risikoen til en aftalt pris og tidsforløb.
Commitment fra involverede parter
Beslutninger bliver foretaget baseret på fakta
Sikring af fælles succes
Øger konkurrenceevnen
Udfordring
Kelsen Group ønskede at fjerne EGA og tunge løft fra en del af deres produktion, samtidig med en besparelse i manpower.
Løsning
BILA har sammen med Kelsen Group udviklet et anlæg, der har en opskærings- og ompalleteringsproces i et og samme anlæg. Anlægget opskærer og åbner smørkartoner, der vejer 25 kg.
Gevinst
Selve opskæringen og optøning tog før ca. 3-4 uger, men nu er EGA fjernet og optøningen kortet ned til blot 36 timer.
Både kunden og BILA investerer i test og analyse i den kritiske fase i starten af et projekt, hvor man typisk danner grundlag for 80% af projektets omkostninger. Får man taget kvalificerede beslutninger i den første fase får man typisk et succesfyldt projekt i den anden ende. Resultatet af et forprojekt er en analyse, test af specifikke opgaver og en rapport med kost og tidsplan på selve opgaven, lavet i tæt samarbejde med den enkelte kunde.
Hele idéen med et BILA forprojekt er at få udarbejdet et grundigt forarbejde af projektet for at skabe tryghed for kunden. Der findes mange eksempler på projekter, der ikke er leveret til den rette kvalitet, kapacitet eller funktionalitet. Ligeledes er der ofte heller ikke leveret til den aftalte tid og pris. Dette hænger ofte sammen med, at opgavens omfang ikke har været klart defineret fra starten, og det er netop dét, BILA vil undgå med et forprojekt.
Konklusionen på et forprojekt kan være, at projektet ikke har attraktiv ROI, teknologien ikke er til stede eller andre forudsætninger, der gør at selve hovedprojektet ikke gennemføres. Men dermed er ’skaden’ begrænset til et mindre beløb, og beslutningen er taget på baggrund af fakta – ikke antagelser.
Kelsen Group – et succesfuldt forprojekt
En af de virksomheder, der har lavet et succesfuldt forprojekt i tæt samarbejde med BILA, er Kelsen Group, der er verdenskendt for sine småkager. På de to moderne bagerier i Danmark bliver der produceret og solgt 25.000 tons småkager om året på 12 produktionslinjer i alt.
Kelsen Group ønskede at fjerne EGA og tunge løft fra en del af deres produktion, samtidig med en besparelse i manpower. Sammen med BILA har de derfor udviklet en ny teknologi, der løser disse udfordringer og er med til at forbedre deres effektivitet og dermed styrke deres konkurrenceevne.
BILA har sammen med Kelsen Group udviklet et anlæg, der har en opskærings- og ompalleteringsproces i et og samme anlæg. Anlægget opskærer og åbner smørkartoner, der vejer 25 kg. Selve opskæringen og optøning tog før ca. 3-4 uger, men nu er EGA fjernet og optøningen kortet ned til blot 36 timer.
Forprojektet gik ud på at verificere den valgte løsning, så det også ville kunne køre i virkeligheden. Helt konkret skulle kniven, der skar smørkartonerne op, testes i BILAs udviklings- og testcenter, for en sikring af at teknologien virkede, og om cyklustiden og dermed kapaciteten også kunne leve op til de krav, som Kelsen havde stillet.
Dette forprojekt blev meget succesfuldt, og derfor blev hovedprojektet også en realitet. Kelsen er nu blevet langt mere konkurrencedygtige, da de nu kan levere ordrer efter få dage, mod tidligere flere ugers leveringstid. Samtidig er arbejdsmiljø, sikkerhed og kvalitet også væsentligt forbedret.
”Samarbejdet omkring forprojektet har virkelig givet ro i maven på valg af løsning, samt sikring af et succesrigt projekt. Nu har vi et system kørende, der lever fuldt op til vores ønsker og krav og ikke mindst brugervenlighed,”
Johan Dissing, Teknisk chef
Få 360 graders rådgivning om dit setup, og lad os hjælpe dig med at tage dine automationsønsker til næste niveau.
Ring til os på +45 97 71 00 44.
Kontakt os
Vi sidder klar til at svare på dine
spørgsmål samt tage en uforpligtende
snak om mulighederne med
produktionsoptimering i din virksomhed.